More optional ideas related to
efficiency...
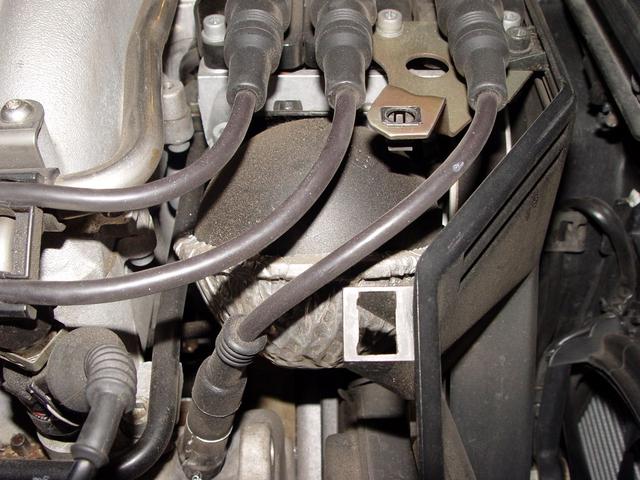
First thing up for me today was to re-locate and fabricate a new vac reservoir. The stock mounting location is terrible for heat, length of vac line and it prevents air from circulating under the intake manifold.
This is what the "new style" reservoir looks like with it's foil-lined under-belly demonstrating the need for insulation on anything exposed to the valley pan area, ESPECIALLY intake runners!! Ya GOTTA know deeper under that manifold it's MUCH hotter than where the vac reservoir is sitting.
Here's my idea on how to get clean, fresh, cool air under and thru...
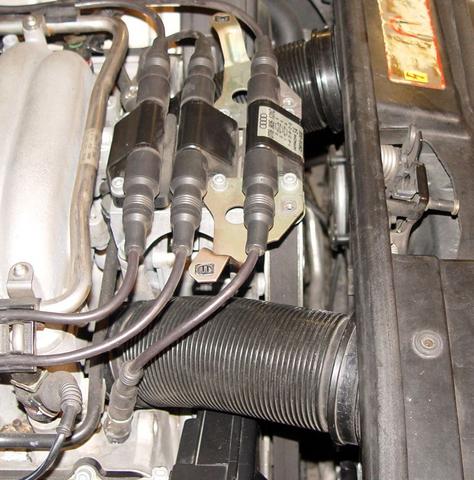
the intake manifold. One on
left side of car will direct air under the IM runners while the right side
one will direct air thru the 'tunnel" section of the IM just below the grid
floor inside the plenum. This will be in addition to the heatshielding and
not an alternative (for me anyway).
I'll need to grind out the left side cold air intake thats in all A4's and
maybe the 90's as well. Then I need to locate some intake ducts that closely
match the inlets in our car and flare to a round outlet. I can always place
directional diffusers in the end of whatever flexible hose I decide to use
for this.
Here's the new vac reservoir...
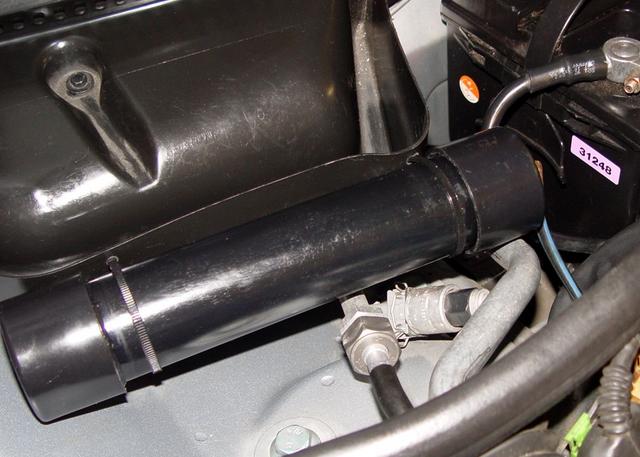
Before I could start making
this piece I needed to "CC" the original reservoir to know volume.
Painstakingly slow process involving a syringe, needle and a calibrated
beaker/burette.
Once I knew the volume for liquid it was a simple matter of deciding on what
size ABS tubing to use. Too small a diameter and it would need to be too
long. Too large a diameter and it couldn't tuck in anywhere or fit between
anything.
I settled on 1.5" I.D. ABS tubing. Glued a cap on one end and poured 350cc's
of liquid inside it. Measured the depth to the bottom and cut the piece to
that length also accounting for end-caps which don't go "all" the way to
their bottom but rather a raised ledge (stop) thats 5/8" up from their
bottom. Pieced it together tightly to re-check volume then dried them off,
drilled a hole in one end cap, tapped it to 1.8" NPT for a 1/8" brass barb
fitting.
Also tested the material in the oven for an hour at 250F to make sure it
wouldn't melt or deform and pulled 20inHg with my vac gun to see if I could
collapse it while hot. Tho the engine bay seldom sees much above 150F I
wanted to err on the side of vast safety margins. Where it's mounted it'll
probably never see much above 100F.
Next I drilled a hole in the firewall and routed the vac line (tomorrow I
need to go buy a rubber grommet to put in that hole). Now the vac line is
only 10"-12" long. Bolted everything up and took it for a spin. Everything
works perfectly.
|