Tis a shame when you have to purchase
something for $132 (shipping inclusive)...
that's supposed to be "plug-n-play" and spend another 5 hours just to make it right. Such is the case with the 6" x 4" velocity stack I bought to do B4 hi-Flo airbox. This thing was SO bad right outta-the-box on flow efficiency that I had 2 choices, ie; attempt to fix it or chuck it. With that said however if I was looking for another one today this one would still be my first choice because in spite of it's shortcomings I still think it's the best out there design-wise of ANYTHING I can currently find. It's rolled inlet edge and radiused taper just completely blow away any/all other VS's I can personally find anywhere. It will out-flow my flow bench so testing it is difficult using the 4" diameter outlet.
However you can see and feel the annular rigdes that are formed in this VS during it's manufacture. This leaves a series of very pronounced ridges/valleys running circumferentially around its ID/OD from inlet to outlet. Not the best anyone can do flow-wise. Additionally when you chuck the VS up in the lathe at either it's inlet or outlet and turn it the TIR is wholly unacceptable. It runs between .187" and .200" TIR and wobbles like a severely bent wheel! And it does that when chucked up in the lathe at either its inlet or outlet... and to make matters worse the TIR eccentricty is not at the same place when chucked at inlet and outlet!
The first thing that must be done is to make a tool that can bring TIR back into just a few thousandths between inlet/outlet. This requires annealing the VS then quenching in ice water to make it "dead-soft" malleable and capable of being bent by inserting a custom turned billet into its outlet end that has a pressed-in handle at it's other end and leveraging the VS into concentricity (bending/deflecting the VS) while the inlet end is held firmly in a 6 jaw lathe chuck. Done carefully/meticulously this can get the ends back within sub .008" axial alignment. From there any remaining TIR can be turned off using the lathe. If one were to try and turn all the initiall TIR out by cutting you'd simply blow thru the tubing wall thickness on one side and end up with a ruined VS. Then when you swapped ends in the lathe chuck you'd do the same thing again at the opposite end you'd blow thru the wall thickness again at a wholly different place.
Once trued up on the lathe with .000" indicated run-out at both ends I can start on smoothing it out and improving on both it's internal ridges and its rolled inlet by both increasing the rolled edge radius and eliminating the OD squared edge that it comes with as well as the "dip" on its inlet side you can see in the "pre-modification" pic to follow.
Bottom line is this is still the best VS I can find off the shelf. But it cannot be perfect until about 4 hours are put into it and a special tool made to gently nudge it back into shape.
The machined section at outlet end of VS in pic is close to where VS outlet will be cut and swaged into a flair just inside airbox so no other possible turbulence causing effects are produced at the outlet as a result.
As I said earlier I cannot flow this on my bench as it exceeds the bench's CFM capabilities. But by placing a 3" diameter restrictor plate under the VS on top of the bench I'm capable of pulling 42CFM more air thru the modified VS than I was capable of getting out of the stock VS. Now of course I won't ever see that kind of flow on my engine but "far better to have it and never use it than need it, even once, and not have it!"
Pre-modification: In this pic you can see
just 2 of many faults associated with this VS...
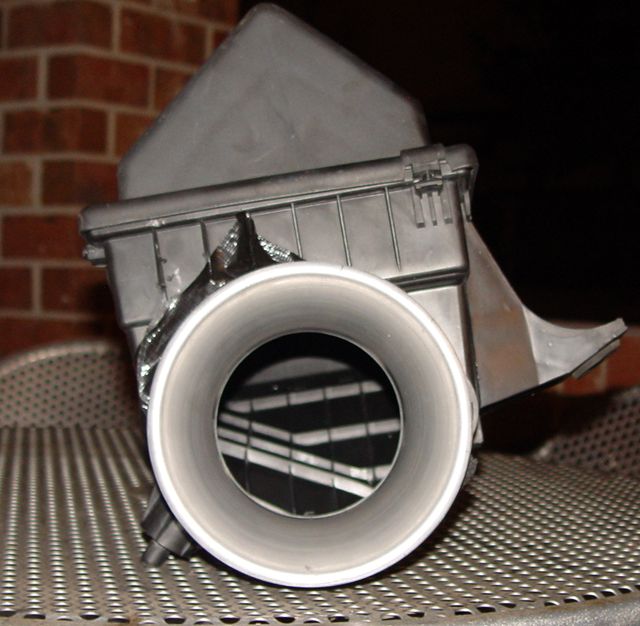
one of which is the radius inlet "dip" just inside the rolled edge and some of the surface undulations running circumferentially around the VS internal diameter from inlet-to-outlet.
Post-modification:
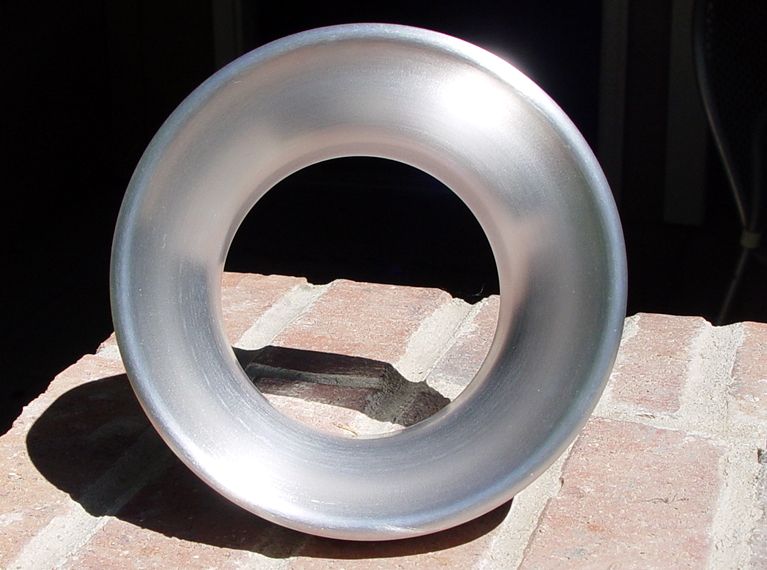
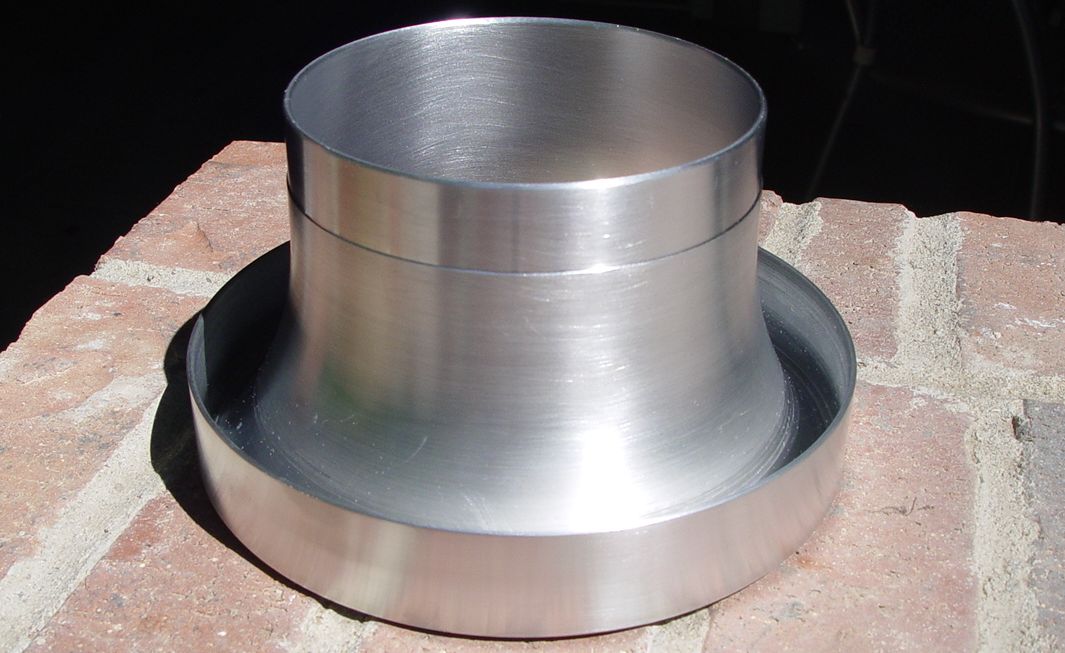
|